Sobre los defectos y métodos de mejora en el proceso de desarrollo de piezas de fundición dúctil
- participación
- Editor
- Lisa
- Tiempo de Publicación
- 2020/5/15
Resumen
Los ingenieros de Yinxiao Machinery registraron los defectos en el proceso de fundición de fundiciones gruesas de hierro dúctil y propusieron las soluciones correspondientes.
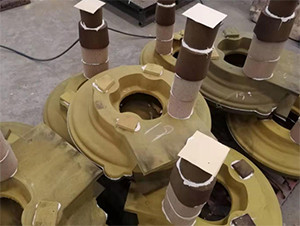
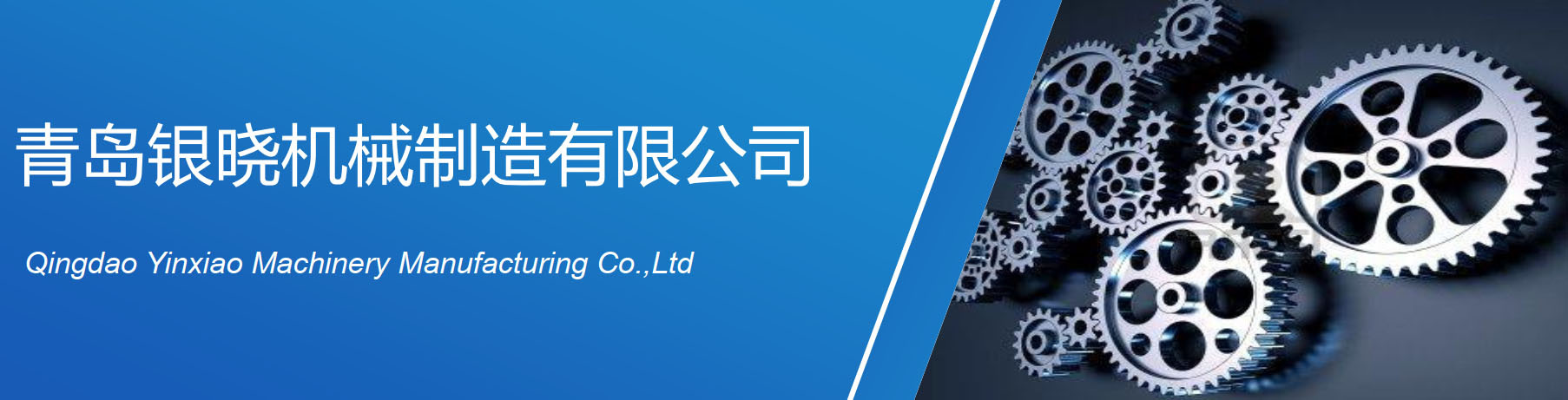
Sobre los defectos y métodos de mejora en el proceso de desarrollo de piezas de fundición dúctil
En junio de 2020, ayudamos a clientes chinos a desarrollar e investigar una fundición de hierro dúctil. Nuestros ingenieros resolvieron y registraron los problemas que ocurrieron durante el proceso de desarrollo, así como sus registros y mejoras.
Resumen:
Con base en la experiencia pasada, se adoptó un plan de proceso similar para piezas maduras y se realizó una simulación de solidificación en el proceso de piezas fundidas recién ensambladas. Los resultados de la simulación muestran que este tipo de esquema similar hace que las piezas moldeadas directamente debajo del bebedero o las piezas moldeadas directamente debajo del tubo ascendente de alimentación y desgasificación, puede haber una cierta probabilidad de porosidad de contracción. Sin embargo, considerando la experiencia adquirida y las características de la expansión por grafitización del propio material de hierro dúctil, se cree que la probabilidad de porosidad por contracción en las piezas fundidas no debería ser muy alta.
Sin embargo, como precaución, se preparó con anticipación un plan alternativo para hierro frío, lo que significa que una vez que la prueba no sea exitosa, se lanzará el segundo conjunto de planes de alimentación de hierro frío para garantizar la compacidad de la organización interna. Después de una ronda de pruebas sucesivas de piezas grandes A y piezas pequeñas C, se descubrió que los esquemas similares originales no podían lograr una aplicación perfecta en este tipo de piezas fundidas. Después de la comparación y el análisis, primero se mejoró el casting C más pequeño, y el resultado fue un éxito perfecto, por lo que la experiencia se copió en los otros dos castings, y el resultado fue una última palabra.
Al mismo tiempo, se adoptó una mejora de proceso similar en una fundición de producto antiguo y también se logró el resultado perfecto. Se puede concluir que el uso completo del elevador de vertido en caliente independiente, el espesor de pared grueso y grande de las piezas de hierro dúctil para facilitar la realización de la solidificación secuencial y el uso completo de las características de expansión de grafitización, para obtener una fundición sólida sin contracción y porosidad. Una de las ideas importantes del diseño del proceso de fundición de hierro.
Prefacio
La característica del proceso de moldeo que elegimos para nuestros clientes es el uso de núcleos de moldes de cáscara de caja caliente de arena recubiertos para hacer la cáscara y formar la cáscara, y usar perdigones de acero para verter. Cuando se recibieron tres tipos de piezas de hierro dúctil con estructuras similares (ver Fundición A con un elevador prefabricado en la Figura 1), se encontró que su estructura y forma eran similares a una variedad producida por la empresa (ver Figura 2 con un elevador prefabricado (partes maduras similares) son muy similares, por lo que para evitar desvíos, el plan de proceso existente se utiliza directamente como referencia y la simulación de solidificación se realiza al mismo tiempo.
Figura 1 Fundición A con elevador de vertido preestablecido
Figura 2 Partes maduras con elevador de vertido
Los resultados de la simulación (ver Figura 3, los resultados y el análisis de la simulación de solidificación de la pieza fundida A) muestran que, aunque hay una porosidad de contracción local, según la experiencia pasada, por ejemplo, piezas similares también tienen porosidad de contracción durante la simulación, pero fundiciones reales No sucedió, creo que debería y no tendrá contracción, y al mismo tiempo aumentar el elevador para mejorar la capacidad de alimentación del elevador. Entonces, la primera ronda de pruebas se llevó a cabo en el gran molde A.
La fundición de prueba encontró una ligera porosidad de contracción después de seccionar (ver Figura 4, hay un estado de porosidad de contracción leve después de seccionar la fundición A), y cuanto más caliente es la contrahuella, más grave es la porosidad de contracción, más fría es la contrahuella, más ligera o incluso completo No. Para la fundición B (la forma es exactamente la misma que la fundición A, pero el tamaño de cada tamaño es más pequeño, el peso es más liviano, los parámetros del diseño inicial del elevador de vertido son exactamente los mismos y la fundición B es no se muestra aquí). Los resultados de la prueba son los mismos que los del casting A.
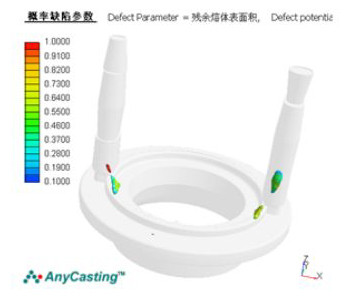
Predicción de defectos de contracción
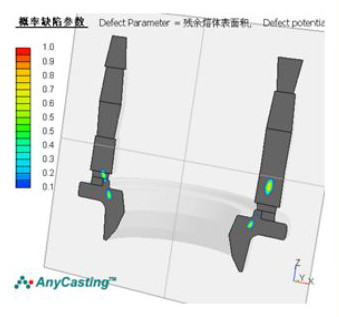
Predicción de defectos de contracción (diagrama de sección)
La figura muestra el resultado de la predicción del defecto de contracción y la figura de la derecha es una vista en sección transversal. En comparación con la dirección de colocación de las piezas fundidas, la ubicación de este plan es más razonable y se recomienda utilizar este plan. Al mismo tiempo, hay una fase líquida aislada durante la solidificación de la fundición, pero el área es pequeña. Además de la autoalimentación de la pieza fundida, la probabilidad de defectos de contracción es pequeña y puede ignorarse.
Figura 3 Resultados de la simulación de solidificación y análisis de la fundición A con elevador prefabricado
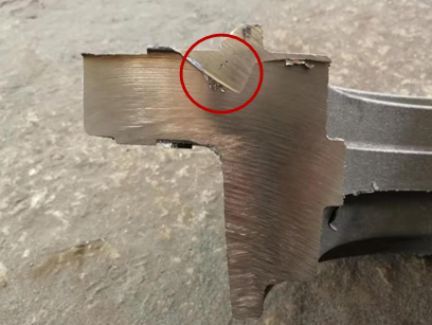
Figura 4 Hay una ligera porosidad de contracción después de cortar el molde A
Luego se llevó a cabo la misma prueba en el tipo más pequeño de fundición C, y los resultados de corte fueron similares, es decir, el interior de las fundiciones con contrahuellas frías y sin contrahuellas era muy denso, mientras que el interior de las piezas directamente debajo de la caliente. las bandas se encogieron. Suelto (vea la Figura 5, hay una ligera porosidad de contracción dentro del tubo ascendente caliente de la fundición C después de seccionar).
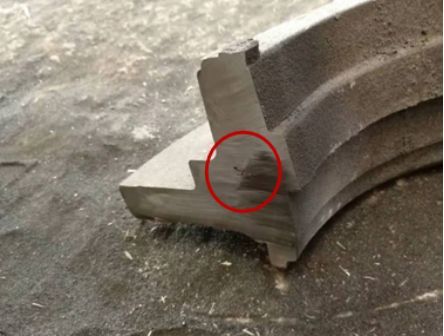
Figura 5 Hay una ligera porosidad de contracción dentro del elevador caliente de fundición C después de seccionar
Y esto está solo por debajo del tubo ascendente caliente, y el rango de volumen de porosidad de contracción es muy pequeño, que obviamente es más pequeño que el de A y B, y dicha porosidad de contracción no es suficiente para afectar la función de uso de la fundición. Por esta razón, se cambió la idea, que es aprovechar al máximo la capacidad de autoalimentación de las piezas fundidas gruesas, abandonar todas las bandas frías y usar bandas verticales de vertido en caliente independientes para las pruebas. Posteriormente, se probó primero en la fundición C y tuvo éxito (la Figura 6 muestra el estado de la fundición vertical C de vertido en caliente independiente que se va a verter con el molde de arena después de la mejora). La misma idea se implementó en la fundición A y la fundición B, y se logró el mismo efecto (la Figura 7 muestra el estado de la fundición vertical A de vertido en caliente independiente en espera de la fundición en arena después de la mejora). Al final, las tres piezas de fundición se desarrollaron y entregaron con éxito, y el segundo conjunto de planes alternativos no se implementó.
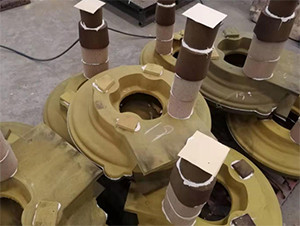
Figura 6 El estado de la fundición vertical mejorada de vertido en caliente independiente C lista para verter arena
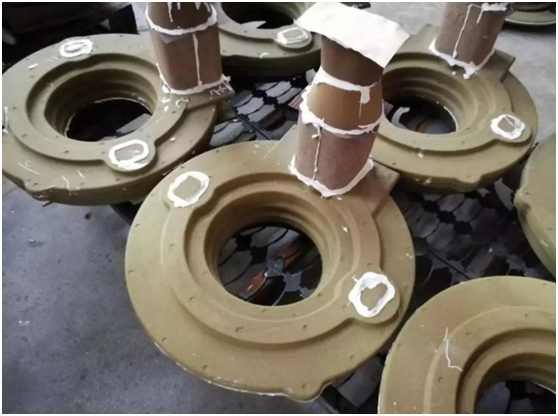
Figura 7 El estado de la pieza fundida A de vertido en caliente independiente mejorada que se va a verter
Análisis de los motivos del fracaso de la primera ronda de ensayos
La información básica de los tres tamaños de fundición y el tubo ascendente de vertido durante la primera ronda de pruebas se muestra en la siguiente tabla.
Material | Tamaño máximo del producto terminado (mm) | Fundición (manta) peso neto KG | Paso térmico máximo mm | Tamaño del cuello del elevador de calor mm | Peso total del elevador KG | Disposición del elevador de vertido | ¿Está abultada la superficie de la caja superior? | Densidad de piezas fundidas | |
Casting A | QT400-18LT | Φ560x168 | 80,5 | alrededor de Φ58 | 60x40 | 23,5 | A verter un riesgo | Presione tres piezas de hierro de caja. La protuberancia desde el costado del elevador de la caja superior hasta el primer escalón es severa | Hay contracción justo debajo del cuello de la contrahuella caliente, leve o nula contracción en la contrahuella fría y no hay contracción en el área sin contrahuella. |
Casting B | QT400-18LT | Φ510x146 | 64,1 | alrededor de Φ48 | 60x40 | 23,5 | |||
Casting C | QT400-18LT | Φ500x138 | 47,2 | alrededor de Φ45 | 50x30 | 22 | Después de presionar tres piezas de hierro de caja, no se encontró ningún abultamiento obvio | ||
Casting maduro | QT450- 10 | Φ480x155 | 64,5 | alrededor de Φ45 | 50x30 | 22 | Fundición interior densa | ||
Observaciones | Debido al uso de núcleos de molde de carcasa de caja de núcleo caliente de arena recubiertos para hacer la carcasa y formar la carcasa, las especificaciones del tubo ascendente están relativamente unificadas, y todo lo anterior está en una forma. |
No es difícil ver en la diversa información anterior que la razón principal del fracaso de la primera prueba debe atribuirse al pequeño cuello del elevador de calor y al pequeño volumen del elevador de calor, por lo que hay contracción debajo del elevador de calor. . ¿Y por qué la contrahuella en frío a veces se encoge? Debido a que el tubo ascendente frío también tiene características similares al tubo ascendente caliente, pasa más hierro fundido por aquí, lo que sobrecalienta la capa de arena, lo que hace que el hierro fundido se disipe lentamente y finalmente se solidifique, y no se puede obtener hierro líquido efectivo. suplemento. Y debido a que el cuello ascendente frío es el mismo que el cuello ascendente caliente, el cuello ascendente no se puede cerrar a tiempo y la expansión del grafito no se puede utilizar de manera efectiva para realizar la autoalimentación. Aunque este tubo ascendente frío y el cuello del tubo ascendente desempeñaron un mejor papel en la extracción y recolección de escoria, debido al tamaño irrazonable, interfirió seriamente con el orden de solidificación del campo de distribución de temperatura, por lo que se produjo la contracción.
Entonces, ¿por qué no se produjeron problemas similares en las partes maduras a las que se hace referencia? A través de una cuidadosa inspección y comparación de los dibujos, se encuentra que la estructura se ve similar, pero de hecho todavía hay ciertas diferencias, como la diferencia en el grosor de la pared entre las paredes adyacentes y el canal de alimentación desde el punto de contacto del elevador y el yeso hasta el extremo distal. En particular, existe una diferencia significativa entre las posiciones de las piezas fundidas A y B donde se coloca el elevador y las piezas fundidas C y maduras, mientras que las piezas fundidas C y maduras son muy consistentes. Por lo tanto, los resultados de la fundición B y la fundición A son similares, y la fundición C es significativamente mejor que la de A y B. La fundición C todavía tiene un cierto grado de contracción, probablemente porque la diferencia en el material y la idoneidad del hierro de la caja de presión han jugado un papel importante.
Además de las diferencias anteriores, además de duplicar ciegamente el proceso, confiar demasiado en la experiencia y negar el riesgo de los resultados de la simulación de solidificación, también hay pequeñas diferencias en el material de las piezas fundidas, hinchazón causada por un peso insuficiente de la pieza. caja de presión del sitio, etc. El efecto combinado de estos factores provocará inevitablemente la aparición de los defectos. Si la contracción no se produce durante la prueba, será un accidente, lo que traerá mayores riesgos para la producción en masa posterior.
Las razones de la contracción de la fundición cerca del cuello del elevador no son más que:
①. Equivalente bajo en carbono de metal fundido;
②. Temperatura de subida baja, solidificación temprana y efecto de alimentación pobre;
③. La ubicación o el tamaño del tubo ascendente no son razonables y el volumen se contrae durante el proceso de solidificación del hierro fundido y no se puede compensar por la pérdida de volumen. La pérdida de volumen se concentra en un lugar para formar cavidades de contracción y la porosidad de contracción se dispersa y distribuye localmente;
④ La forma o el área de la sección transversal del cuello del elevador no es razonable y el canal de alimentación está bloqueado, por lo que el elevador no cumple una función de alimentación.
Puede verse que la porosidad de contracción de la pieza fundida cerca del cuello del elevador también está en línea con los puntos anteriores.
Medidas básicas y resultados para evitar la porosidad de contracción de las piezas fundidas en el tubo ascendente
De acuerdo con las contramedidas básicas para resolver la contracción del cuello del elevador, que incluyen:
①. Cambie la posición o la forma del tubo ascendente y cambie la secuencia de solidificación para que las partes de contracción que no se pueden compensar puedan compensarse y se pueda eliminar la contracción o contracción.
②Coloque la plancha fría en la posición adecuada.
③Cambie la posición de la puerta interior para obtener un campo de temperatura razonable y una secuencia de solidificación.
④ Aumente el volumen de la contrahuella.
⑤Ampliar (o reducir) el cuello del elevador.
⑥Utilizando el método integrado de vertido y elevador para aumentar la temperatura del elevador.
Al mismo tiempo, en combinación con el análisis anterior, se decidió realizar inmediatamente otra prueba en C en buenas condiciones. Es utilizar un tubo vertical de vertido independiente como se muestra en la Figura 6. El cuello del tubo ascendente de calor y los parámetros del tubo ascendente de calor permanecen sin cambios, el tubo ascendente de salida se cancela y la caja de presión original La plancha se aumenta de 3 a 5 piezas pieza pesa 30 kg) para seguir manteniendo la rigidez suficiente del molde de arena, mientras aumenta el carbono del hierro fundido original en un 0,1%, y el silicio del hierro fundido original sigue manteniendo un valor bajo (mantener bajo el valor de impacto). El resultado de la prueba es que la pieza fundida no tiene poros debido al tubo ascendente de vertido independiente y no hay una pequeña porosidad de contracción en la pieza fundida; la estructura de la carrocería de la sección sin la contrahuella también es densa, por lo que el esquema es completamente efectivo.
Sobre esta base, se adoptó un esquema similar para las piezas fundidas A y B, es decir, el elevador caliente y el cuello del elevador se incrementaron respectivamente, y la posición de entrada de hierro fundido se cambió debido al aumento de estos parámetros, el elevador frío original fue cancelado, y el hierro de la caja de presión se incrementó de 3 a 7. Las otras medidas fueron las mismas que las de C. Como resultado, los problemas originales de A y B desaparecieron y se resolvió la contracción. La posterior producción en masa también confirmó plenamente todos los análisis antes mencionados y las medidas efectivas adoptadas. Consulte la tabla a continuación para ver algunos parámetros específicos después del cambio:
Material | Tamaño máximo del producto terminado (mm) | Fundición (manta) peso neto KG | Tamaño del cuello del elevador de calor mm | Peso total del elevador KG | Disposición del elevador de vertido | ¿Está abultada la superficie de la caja superior? | Densidad de piezas fundidas | |
casting A | QT400-18LT | Φ560x168 | 80,5 | 70x60 | 25 | Elevador de un disparo | Presione siete piezas de caja de hierro | Sin contracción |
casting B | QT400-18LT | Φ510x146 | 64,1 | 70x60 | 25 | |||
casting C | QT400-18LT | Φ560x138 | 47,2 | 45x28 | 14 | Presione cinco piezas de caja de hierro |
Promoción y aplicación de experiencias similares
Con base en la experiencia mencionada, infiera otras cosas, se mejoró rápidamente otro lanzamiento (peso neto 156Kg). Las figuras 8 y 9 a continuación muestran el proceso original de esta fundición, utilizando elevadores de vertido en caliente independientes, moldes de arena con orificios de ventilación y tapas de fundición. El contraste del estado de fundición de la boca. Los resultados de la prueba son muy buenos resultados y muy buenos beneficios económicos. La tasa de producción de esta pieza de tecnología ha aumentado en un 12% en comparación con la tecnología original, y la tasa de contracción y desperdicio después del procesamiento se ha reducido del 20% a 0.
Se puede ver que, haciendo un uso completo del elevador de vertido en caliente independiente, haciendo un uso completo del grueso y gran espesor de pared de las piezas de hierro dúctil para facilitar la solidificación secuencial y haciendo un uso completo de las características de expansión de grafitización para obtener una fundición sólida sin contracción. Es hierro dúctil. Una de las ideas importantes del diseño del proceso de fundición.
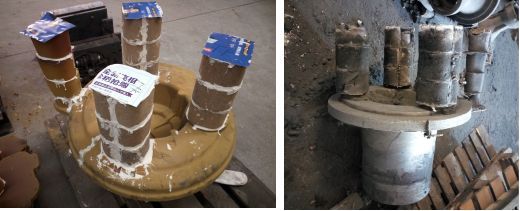
Figura 8 El proceso original del molde de arena y el estado de fundición del elevador que se va a verter
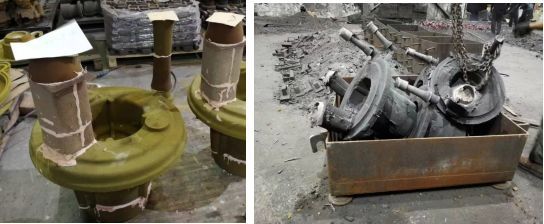
Figura 9 Piezas fundidas con elevadores de vertido en caliente independientes, moldes de arena con orificios de ventilación y piezas fundidas con elevadores de vertido